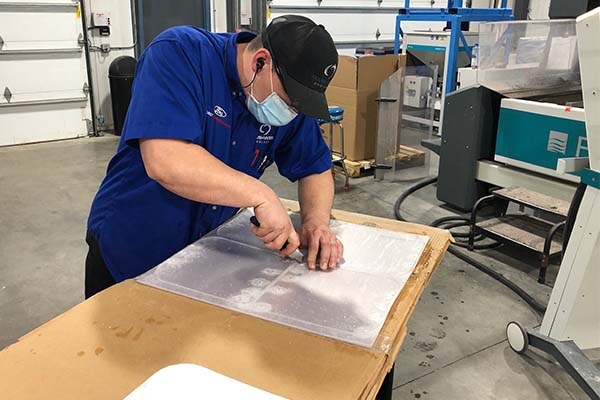
02 Jul Roush Yates Engines: ‘Technology allowed us to adapt quickly and manufacture for different industries’
In RKL eSolutions’ Your Story series, they speak to senior business leaders about the challenges they’re facing and the steps they’re taking to overcome them. Todd English, the vice president of marketing and strategic partnerships at Roush Yates Engines, talks about how Roush Yates Engines and Roush Yates Manufacturing Solutions businesses are dealing with the coronavirus disruption and offers advice that could help your company. Roush Yates Engines uses Sage X3, which supports greater efficiency, flexibility, and insight.
I work for Roush Yates Engines in Mooresville, North Carolina. We build, design, and develop high-performance race engines for various performance teams in the NASCAR and IMSA race series.
As the exclusive engine builder for Ford Performance – the high-performance division of Ford Motor Company – we have powered race teams to championships and wins at crown jewel events like Daytona 500, and the 24 Hours of Le Mans. We have two facilities located in Mooresville, North Carolina, and all of our 200 employees work on-site.
All businesses typically have some type of contingency plan, but the challenge with coronavirus is that there wasn’t a playbook. Although it was a huge blow to begin with, we have learned so much with diversification of our advanced manufacturing facility which provided support and jobs to our workforce, families, and communities.
We ultimately worked to get the racing side of the business back up and running again, and our engine manufacturing facility recently reopened.
Invest in technology to diversify your services
At Roush Yates Engines we realized early on that it was more cost-effective and efficient to machine our own high-performance components for our engines. This skillset could then support other industries if needed. This is why we formed a division called Roush Yates Manufacturing Solutions, which uses state-of-the-art equipment and a vertically integrated supply chain to supply the high-precision engine components we need to support our internal engine builds as well as other industries.
We specialize in Computer Numerical Control (CNC) manufacturing, which is a method for automating control of machines using software embedded in a microcomputer attached to the tool. The technology is fascinating and exciting. CNC machines are constantly evolving and require capital investment. We have over 50 advanced CNC machines, for example.
There is a lot of functionality within these machines that allow us to switch quickly between different industries. We can switch machines that might be machining defense parts one day, and the following day is machining medical components. Technology has allowed us to adapt to various industries very quickly.
Although our experience is rooted in automotive and motorsports, we understood that our CNC manufacturing skills could apply to machining components for other industries. Accordingly, we have diversified into aerospace, defense, medical, aviation, and other high-tech industries. We are an AS9100 certified company, which means we meet the requirements to build safe and reliable products according to civilian and military aviation requirements.
We were fortunate that our facilities were able to remain open after the state issued stay-at-home orders during COVID-19. We were able to move employees working on high performance engines to our manufacturing facility to support the defense industry during the pandemic, hence essential business.
We offered services or products that could of use during a pandemic, working with various companies to produce products for healthcare professionals – this included face masks, face shields, aerosol cabinets, and ventilator components.
Help your suppliers to forecast demand and mitigate issues
From a financial standpoint, our manufacturing facility continued day-to-day operations. It has been up-and-running and doing business to support the healthcare sector and others during this pandemic. This diversification has assisted with cash flow, as well as keeping everybody employed.
But we did look at our business units to determine how we could control costs and acted on some of these initiatives to be on the safe side. We also took advantage of federal assistance through the CARES Act.
We immediately reached out to our suppliers to identify which ones potentially might have concerns or issues or trouble to supply demand. There was a lot of communication back and forth, which was assisted by today’s technology platforms such as Zoom, Webex, etc. So for us, we did not have any supply chain concerns, because of constant communication and ability to pre-order some of our materials.
With some of the suppliers we reached out to, we ordered maybe two or three months worth of supplies to ensure that we could maintain our particular commitment. Overall, I think our supply chain has been a success, as we have been able to lean on our suppliers, help them with forecasted demand and assist them with operating and getting back up to speed.
We also have to give the State of North Carolina and Iredell County a lot of credit. They helped a lot of manufacturers that support various industry, so they could continue and work to supply materials for our high-performance engines and other defense, aerospace, and health care industries.
My top three takeaways
Here’s what’s worked best for our business.
1. Diversify your services
We were able to shift our engine production to create resources in trying to help out our country, maintaining work for everybody at Roush Yates Engines, without having to furlough anyone within the organization.
We were very fortunate that we were able to continue manufacturing various components for our first responders and healthcare professionals, which allowed us to keep our employees on the payroll and continue moving forward during this coronavirus crisis.
2. Prioritize your people
People are our most significant assets. Our people worked well within the new system, listening to recommendations from the state and of the federal government. That has allowed us to get through these unprecedented times. One of our top priorities was to keep people employed, and I’m glad to say we achieved our goal of not having to lose or furlough anybody.
3. Take advantage of technology
Technology allowed us to shift work from engines to other types of manufacturing very quickly, allowing us to create products which were useful in our pandemic situation. As well as supporting us with communication, it also assisted us when it came to maintaining our supply chain, which was vital for us and other businesses to keep going.
Todd English spoke with Sage Advice’s Asavin Wattanajantra